Porosity in Welding: Identifying Common Issues and Implementing Finest Practices for Prevention
Porosity in welding is a pervasive concern that often goes undetected till it creates considerable problems with the integrity of welds. This usual flaw can jeopardize the strength and resilience of bonded structures, posturing safety and security dangers and resulting in costly rework. By recognizing the root causes of porosity and applying efficient prevention approaches, welders can substantially boost the high quality and reliability of their welds. In this conversation, we will discover the essential factors adding to porosity formation, analyze its harmful results on weld performance, and review the most effective techniques that can be adopted to minimize porosity occurrence in welding processes.
Typical Reasons For Porosity
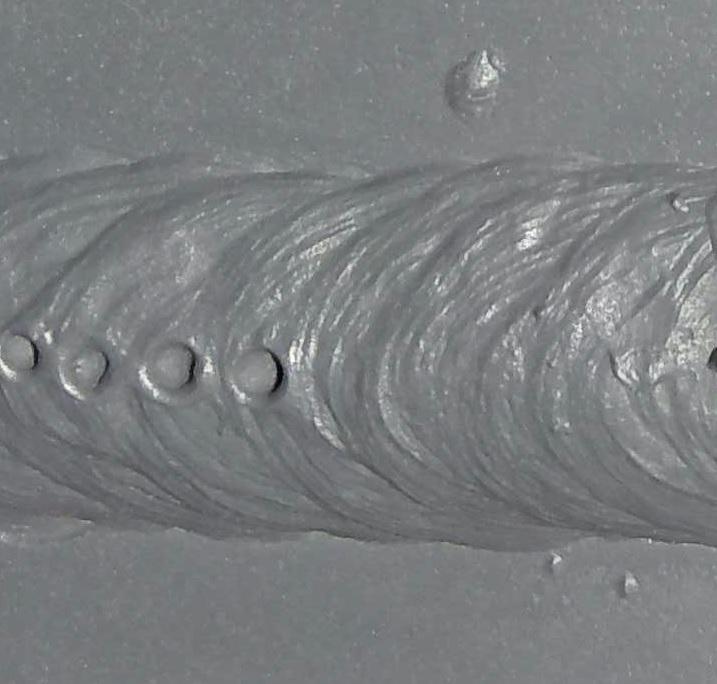
Utilizing filthy or wet filler materials can introduce contaminations right into the weld, adding to porosity problems. To reduce these usual reasons of porosity, extensive cleaning of base steels, appropriate shielding gas choice, and adherence to optimal welding criteria are vital practices in attaining top notch, porosity-free welds.
Impact of Porosity on Weld Top Quality

The existence of porosity in welding can dramatically compromise the structural stability and mechanical residential properties of bonded joints. Porosity creates spaces within the weld steel, damaging its overall stamina and load-bearing capability.
Welds with high porosity levels often tend to show reduced effect strength and decreased ability to deform plastically prior to fracturing. Porosity can restrain the weld's capability to efficiently transmit forces, leading to early weld failure and potential safety threats in important frameworks.
Best Practices for Porosity Prevention
To boost the architectural integrity and high quality of bonded joints, what details measures can be carried out to decrease the occurrence of porosity during the welding process? Utilizing the proper welding strategy for the specific material being welded, such as changing the welding angle and weapon placement, can better prevent porosity. Normal inspection of welds and immediate remediation of any problems determined during the welding process are vital methods to stop porosity and generate high-grade welds.
Relevance of Correct Welding Methods
Carrying out proper welding strategies is vital in ensuring the architectural like it integrity and top quality of welded joints, constructing upon the structure of efficient porosity avoidance actions. Too much warm can lead to boosted porosity due to the entrapment of gases in the weld swimming pool. Additionally, using the ideal welding parameters, such as voltage, present, and take a trip rate, is critical for achieving audio welds with very little porosity.
Moreover, the choice of welding procedure, whether it be MIG, TIG, or stick welding, should line up with the details demands of the task to make certain optimum outcomes. Appropriate cleansing and prep work of the base metal, in addition to picking the best filler product, are additionally vital parts of competent welding techniques. By adhering to these finest techniques, welders can minimize the danger of porosity development and generate top quality, structurally sound welds.
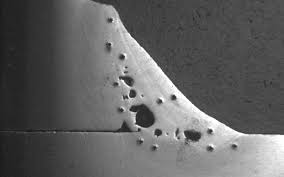
Checking and Quality Assurance Procedures
Examining treatments are important to discover and stop porosity in welding, making sure the toughness and longevity of the last item. Non-destructive testing techniques find more such as ultrasonic testing, radiographic testing, and visual inspection are generally used to recognize prospective flaws like porosity.
Post-weld assessments, on the various other hand, evaluate the last weld for any flaws, consisting of porosity, and confirm that it satisfies defined standards. Applying a detailed quality control strategy that consists of comprehensive testing treatments and inspections is critical to minimizing porosity issues and guaranteeing the general top quality of bonded joints.
Conclusion
To conclude, porosity in welding can be a common problem that influences the quality of welds. By identifying the typical sources of porosity and applying ideal practices for prevention, such as proper welding methods and testing procedures, welders can make certain top quality and dependable welds. Click Here It is important to prioritize prevention techniques to lessen the event of porosity and keep the honesty of bonded frameworks.